NASA has tested a kind of super-fridge that may hold the key to any future crewed mission to Mars. Without the new cryogenic cooler, a ship to Mars would reach the Red Planet with empty fuel tanks, which would ruin everyone’s day.
The idea of seriously designing an expedition to put astronauts on Mars has been kicking around for well over 70 years and is taken very seriously in certain quarters today. However, the devil, as they say, is in the details.
It’s one thing to design a vehicle to get to Mars, its engines, life support systems, sensors, navigation instruments and so forth, but at the heart of it all are the hard numbers of where to get the power to push it from Earth to Mars and back home again. If it’s using chemical rockets, that reduces the question to the type of fuel used to provide thrust.
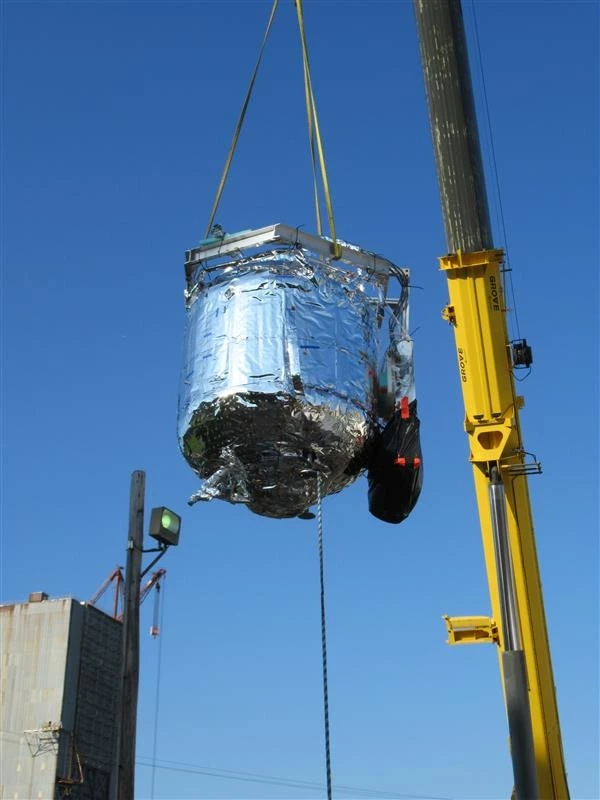
NASA/Kathy Henkel
For most deep space missions thrust isn’t too much of a problem once the mission is underway. The big changes in velocity are provided by the boosters that lifted the probe off the Earth and after that it’s a matter of simple ballistics. For course corrections and other small changes in trajectory, small thrusters fueled by relatively stable liquid and gases will do. Even the ion thrusters that have been used more often in recent years use propellants like xenon that don’t need much looking after.
The point of this is that robotic probes weigh comparatively little and can take years or even decades to reach their destination, so thrust and speed aren’t big factors. However, where humans are concerned, the mission length has to be kept as short as reasonably possible and the mass of the ship large enough to keep the crew alive and well.
That means using the most efficient fuel possible and that means large tanks filled with liquid hydrogen, oxygen, or methane. The problem is that these are all cryogenic liquids, with liquid hydrogen boiling at -252.9 °C (-423.2 °F), liquid oxygen at -183 °C (-297.4 °F), and -161.6 °C (-258.9 °F). It also means that even in the freezing cold of space these cryofuels don’t want to stay put. They want to and do boil inside their tanks, which have to be vented to allow the gases to escape and prevent the tanks from exploding.
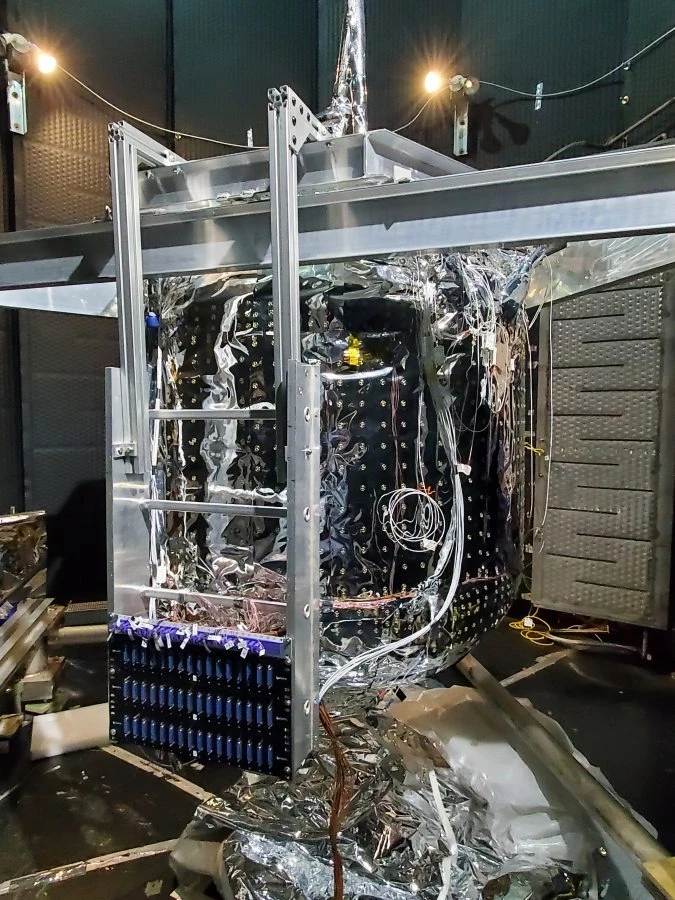
NASA/Kathy Henkel
That might be fine for a rocket sitting on the pad or missions lasting less than a week, but for a Mars mission lasting over two years, that’s a real problem. If we run the numbers, the results are more than a little depressing. If the Mars ship has a large, lightly insulated tank holding 38 tonnes of liquid hydrogen, it’s estimated that the passive boil-off would cost about 16 tonnes per year.
In other words, the Mars mission would see the crew arriving at its destination without the fuel to get home.
Thick insulation can reduce the losses, though they would still be unacceptably high. Therefore, NASA is working on its Cryogenic Fluid Management Portfolio Project, which is tasked with developing a system of state-of-the-art insulation and active cooling that aims at zero boil-off over months and even years, as well as improved systems for handling cryogenic fuels without loss.
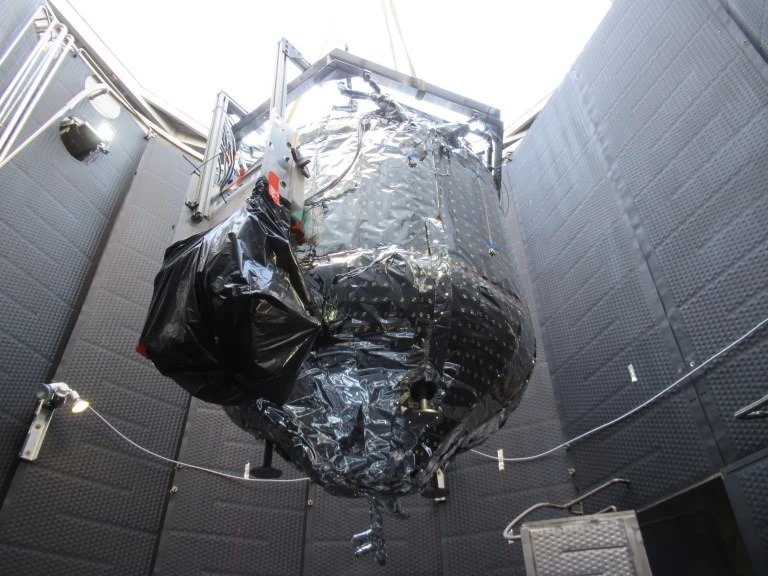
NASA/Kathy Henkel
At NASA’s Marshall Space Flight Center in Huntsville, Alabama, engineers installed what’s called a two-stage cooling system on a test stand for a three-month trial. Also called “tube on tank” cooling, this consists of two cooling loops embedded in thick metalized insulation and a heat shield.
In the primary cooling loop, tubes full of liquid helium cooled to -253 °C (-424 °F) are wrapped around the cryogenic propellant tank to directly cool it and its contents. Over this are layers of insulation and a second loop carrying slightly warmer helium at -183 °C (-298 °F) set behind the heat shield that covers that entire assembly. This loop intercepts and rejects all incoming heat before it can penetrate any further.
The result is a system that can keep propellants supercooled indefinitely so long as there’s power to run the cryo-refrigeration machinery. That not only means avoiding the embarrassment of showing up at Mars without a ride home, but the ability to do without unneeded fuel surplus and to plan longer duration missions.
“Technologies for reducing propellant loss must be implemented for successful long-duration missions to deep space like the Moon and Mars,” said Kathy Henkel, acting manager of NASA’s Cryogenic Fluid Management Portfolio Project. “Two-stage cooling prevents propellant loss and successfully allows for long-term storage of propellants whether in transit or on the surface of a planetary body.”
Source: NASA